Als ich angefangen hatte, hab ich gedacht, es wär ganz einfach. Aber da hatte
ich mich ziemlich geirrt. Angefangen hab ich ca. am 01.03.05 und fertig bin ich
am 10.05.05 geworden.
Hört sich lang an, allerdings hab ich auch nicht ununterbrochen daran gearbeitet, sondern
noch tausend Sachen nebenher gemacht. An einem Wochenende oder gar Tag ist das trotzdem
nicht zu schaffen.
Materialien:
- MDF Platten in der gewünschten Größe
- Ein paar Restholzstücke zur Formgebung
- Dämmmaterial (Bitumenmatten, Bitumenstreichmasse)
- Leder in der gewünschten Farbe (z.b. vom Autosattler)
- Lederkleber (am Besten auch vom Sattler)
- Polyesterharz (ca 5kg)
- Feinziehspachtel (auch ca. 5kg)
- Formflies
- Glasfasermatten (1qm reichte bei mir aus)
- Schleifscheibe für eine Flex
- viel Schleifpapier bis ca. 120er Körnung
- Staubmaske!!!!!
Werkzeug:
- Flex (sehr zu empfehlen!)
- Elektrotacker
- gaaaaanz viele Billigpinsel (die sind nämlich anschließend steinhart!)
- Heißluftfön
- mehrere Spachtel (teilweise müssen die nachher weggeworfen werden)
- Bohrmaschine, Heißklebepistole und sonstiges Standardwerkzeug
Zeit:
lange, sehr lange (fand ich)
1. Dämmung der Türen & spätere Montage der Doorboards
Sollte der favourisierte Einbauort ein Golf II sein, empfehle ich dringend
die Türen zu dämmen. Ich habe mir dafür im Internet selbstklebende Bitumendämmmatten
geholt. Allerdings hätte man sich das selbstklebend sparen können. Hab sie letzendlich
mit Silikon an die Tür gebappt.
Da das noch nicht so richtig hielt und noch viele Zwischenräume waren, hab ich mir aus
dem Obi einen 5kg Eimer "Bitumenspachtelmasse" geholt. Das hab ich dann schön über die
Matten verteilt. Den Spachtel, den ich dafür benutzt hab, hab ich anschließend zusammen
mit dem Eimer entsorgt. Der war nicht mehr zu retten. Weiterhin empfehle ich Handschuhe
zu benutzen. Ich hab das leider nicht gemacht und hab drei Tage noch Spass an schwarzen
Fingern gehabt.
Die roten Kreise markieren die späteren Befestigungslöcher für das Doorboard.
Auf der anderen Seite habe ich eine Holzleiste aufgeklebt, in diese habe ich Einschlagmuttern
geschlagen (vorher Loch bohren) und dann noch zusätzlich mit Montagekleber festgeklebt. Das fest-
kleben ist dringend zu empfehlen, da man keine Chance hat die Einschlagmuttern gegenzuhalten und
vor einem herausdrücken durch die eventuell schief eingedrehten Schrauben von vorne zu bewahren.
Dort wo die Schrauben sind, waren beim Golf II schon Löcher, allerdings habe ich die trotzdem
nochmal mit Grundierung behandelt, damit es nicht rostet.
Auf den Fotos fehlt noch die Spritzfolie, um das Wasser aus dem Auto zu halten. Diese muss auch
unbedingt unten gut verklebt werden, sonst hat man Wasser im Auto!
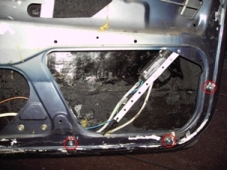
|
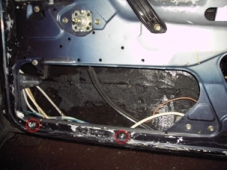
|
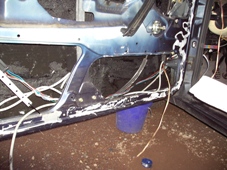
|
rechts (hinten) |
rechts (vorn) |
links |
2. Der Doorboardbau
Angefangen habe ich damit, mir eine Tür zu besorgen. Der Vorteil daran ist, dass man im Keller arbeiten kann
ohne, dass man ständig am Auto hocken muss.
Den Rest erklären die Bilder, denke ich.
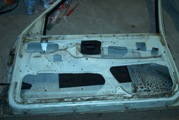
|
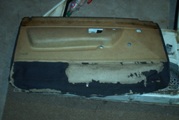
|
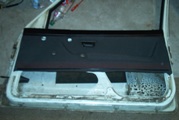
|
1. Die extra Tür |
2. die abgesägte Pappe (hinten) |
3. die abgesägte Pappe (vorne) |
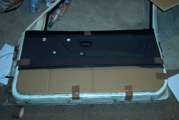
|
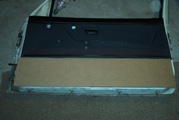
|
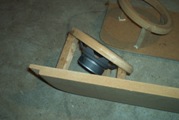
|
4. ein Karton zum Anpassen |
5. Das Brett (schon ziemlich passend gekauft) |
6. angewinkelte Boxen |
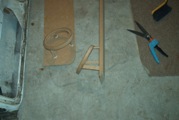
|
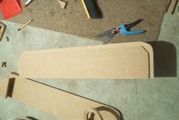
|
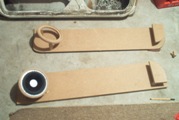
|
7. links & rechts nebeneinander |
8. gefräste Nut |
9. Gesamtansicht |
zu 2 & 3
Ich hab mir eine zweite Türpappe besorgt (genau wie die Tür) und hab die mal auf gut Glück abgesägt
Vorher hab ich den Stoff von der Türpappe abgezogen.
zu 4
Um das Brett später besser zusägen zu können, hab ich einen Rohling aus Pappe angefertigt.
zu 6 & 7
Damit die Boxen später nicht nur unten in den Fußraum schallen, hab ich die Ringe, wo später die Boxen
montiert werden, angewinkelt
zu 8
um später Formfließ und Leder festtackern /-kleben zu können, hab ich eine Nut gefräst. Allerdings hab ich
die Nut zu tief gefräst. 5mm sollten eigentlich ausreichen.
zu 9
Das ist die Gesamtansicht.
Leider ist es aber doch so noch nicht ganz komplett. An der einen Ecke hab ich schon eine Rundung aufgeleimt, damit
man das Flies später besser spannen kann.
Zwischen dem Boxenring und der Rundung hab ich auf jeder Seite noch auf der selben Höhe wie die Rundung eine
Holzleiste auf kleinen Holzfüßen aufgeleimt, weil sich sonst das Flies nicht richtig spannen ließ.
Wenn man das selber so macht, weiß man was ich meine (das zu erklären ist was doof).
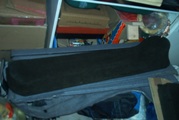
|
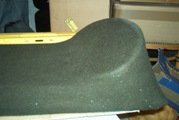
|
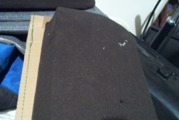
|
10. Gesamtansicht mit Flies |
11. Vorderer Teil mit Flies rund um die Box |
12. hinterer Teil mit Flies bespannt (oben hab ich ein Loch wieder zugenäht) |
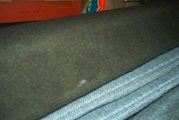
|
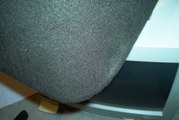
|
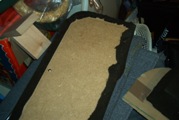
|
13. Einkerbung zum Festschrauben (unten) |
14. Einkerbung zum Festschrauben (Ecke) |
15. Ansicht von hinten (1) |
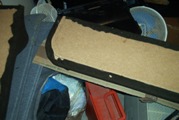
|
16. Ansicht von hinten (2) |
zu 10
So sieht das Board bezogen aus
zu 11
Hier das Flies rund um die Boxenaussparung. Vorne erkennt man die schräg nach hinten laufende aufgeleimte Leiste
zu 12
oben sieht man ein zugenähtes Loch, das durch nen Schraubenzieher entstanden ist. Später sieht man davon aber nichts mehr.
zu 13 & 14
Hier hab ich das Flies mit Heißkleber auf das Holz aufgeklebt, damit ich dort später das Doorboard festschrauben kann
Leider hab ich nicht bedacht, dass meine Aussparung viel zu klein sind. Würde also jedem empfehlen, die Aussparungen größer
zu machen. Das später einzufügen, ist extrem ungünstig. Naja es geht aber, dazu später mehr.
zu 15 & 16
Hier erkennt man, wie ich das Flies in der Einkerbung festgetackert habe. Man sollte tunlichst alles sauber zurecht schneiden
wenn das Flies durch das Harz erstmal hart ist, wird das unverhältnismäßig viel schwerer und nur mit grobem Werkzeug möglich
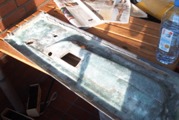
|
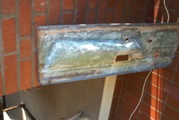
|
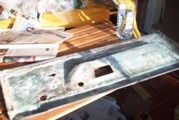
|
17. vertärkte Türpappe (1) |
18. vertärkte Türpappe (2) |
19. vertärkte Türpappe (3) |
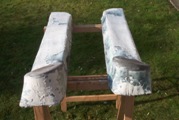
|
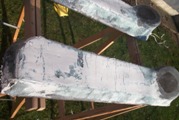
|
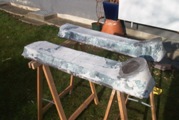
|
20. erstes grobes Spachteln (vorne) |
21. oben |
22. Seite (1) |
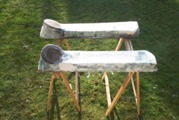
|
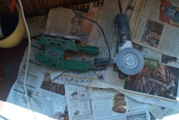
|
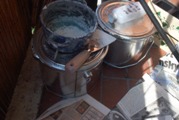
|
23. Seite (2) |
24. Mein hauptsächlich benutztes Werkzeug |
25. Die Teile die ich zum Anmischen gebraucht hab |
zu 17 - 19
Da die Türpappen des Golf II ziemlich "wabbelig" sind, hab ich die mit ein paar Matten Glasfaser und Polyesterharz verstärkt
zu 20 - 23
Leider habe ich keine Bilder vom Tränken des Flieses mit dem Harz, aber da man sich dabei ziemlich einsaut, müssen diese Bilder herhalten
Ich habe schon die erste Schicht Spachtel aufgetragen. Da ich leider beim Flies ziemlich ungenau war, muss ich das nun durch entsprechend
viel Spachtel und schleifen wieder ausbessern. Auf den Bildern kann man dem Spachtel gerade beim Trocknen zusehen.
zu 24
Meine beiden "Lieblingswerkzeuge". Die Flex mit der Schleifscheibe ist extrem effektiv bei großen Unregelmäßigkeiten, wird aber schon ziemlich
gut. Die Schleifmaschine ist dann für den Rest, um nicht alles mit der Hand schleifen zu müssen.
Wenn man nun mit der ersten Schicht fertig ist, folgen dann weitere Schichten, biss man keine gröberen Unregelmäßigkeiten mehr feststellen kann
Wenn man mit Leder bezieht, dann können Löcher schon bis zu 2mm tief sein, ohne, dass man davon später etwas sieht. Bei Hubbeln muss man nochmal
mit der Feile ran.
Dringend empfehle ich sowohl eine Schutzbrille als auch eine Staubmaske zu tragen, die Staubwolken die insbesonder beim Schleifen mit der Flex
entstehen sind sicherlich nicht besonders gesund.
zu 25
Zum Anmischen des Polyesterharzes und des Spachtelmasse habe ich einen alten Topf verwendet. Anschließend kann man das verwendete Material wie
Spachtel, Pinsel, Rührer etc. übrigens wegwerfen.
In dem einem Eimer ist das Polyesterharz, in dem anderen die Spachtelmasse. Oben drauf liegt der Härter
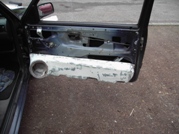
|
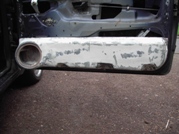
|
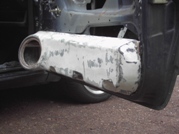
|
26. eingebaute rechte Seite |
27. eingebaute rechte Seite |
28. rechts von der Seite |
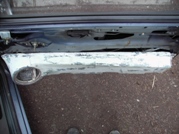
|
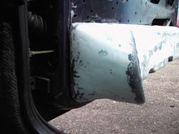
|
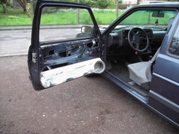
|
29. rechte Seite von oben |
30. rechte Seite, Boxenaussparung |
31. nun links |
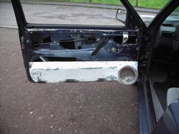
|

|
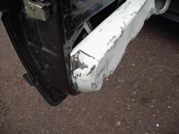
|
32. nochmal links |
24. links oben |
25. links hinten (obere Ecke) |
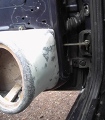
|
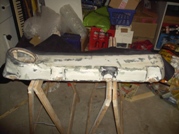
|
35. links, blick auf Boxenaussparung |
36. rechts nochmal ausgebaut |
zu 26 - 35
Jedes Bild einzeln zu erklären wäre jetzt ziemlich dämlich, deswegen muss die Gesamheit herhalten
Auf diesen Bildern kann man sehr gut erkennen, wie die Doorboards modifiziert wurden.
Die Aussparungen für die Schrauben sind deutlich größer geworden
Anfänglich hatte ich dafür einen wesentlich kleineren Bereich vorgesehen, doch dies erwies sich als
schlecht, da sich das Doorboard nicht montieren ließ. Deswegen habe ich irgendwann die Aussparungen
deutlich vergrößert.
Hierfür habe ich ein Loch in der entsprechenden Größe an der richtigen Stelle gesägt bzw. geflext
Anschließend habe ich mühsälig das Formfließ eingeklebt. Der restliche Teil sollte soweit ja klar
sein, es folgt laminieren, spachteln, schleifen usw.
Hier auf den Bildern sind die Doorboards schon komplett geschliffen. Zwar sind noch einige "Löcher"
in der Spachtelmasse geblieben, da diese aber nur ca. stecknadelkopfgroß sind, fällt dies beim Beziehen
mit Leder nicht auf. Insgesamt kann man sehen, dass das Doorboard überall komplett anliegt und nicht wackelt.
Durch die Schraube die außen oben eingedreht wird, wird das Doorboard daran gehindert in irgendeiner Weise
nach vorne zu kippen.
Wie man gut erkennen kann blieb im hinteren Teil noch ein kleiner Spalt. Der reichte gerade aus, dass ich meine
Hand/Arm durchstecken konnte und ausgedrehte Einschlagmuttern gegenhalten konnte. Nochmal der Tipp, es ist dring-
end zu empfehlen die Muttern mit starkem Montagekleber festzukleben. Dies geht am besten, indem man die Mutter
mit Kleber an den Zacken benetzt anschließend in das vorgebohrte Loch steckt und von vorne mit einer Schraube
festzieht. Empfehlenswert ist es hierfür das Doorboard vorerst noch weg zu lassen.
zu
zu 36
Hier nochmal ein Blick auf die nachträglich eingebauten Ausparungen für die Schrauben
Die zweite Aussparung von rechts ist mir am besten gelungen. Hier war nur noch sehr wenig Spachtel nötig um die
perfekte Form hinzubekommen.
An der Aussparung ganz links ist übrigens nach oben hin wenig Platz. Dies macht später ein bisschen Probleme mit
einem dicken knubbeligen Schraubenzieher. Aber ich hab es ja gemeistert.
ohne Bild
Zwischenzeitlich habe ich noch die Kabel eingebaut. Hierfür habe ich ein ca. 30cm langes Stück Kabel durch ein
vorher gebohrtes Loch gezogen. Anschließend habe ich das Loch wieder mit Montagekleber verklebt, damit das Door-
board wieder dicht wird. Wie das geht, sollte aber auch ohne Bild verständlich sein.
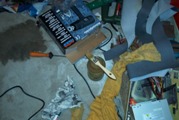
|
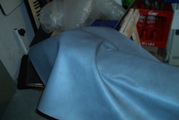
|
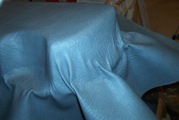
|
37. Der Kleber und die ganzen Utensilien |
38. schon soweit angeklebt, die Erhöhung ist die Box |
39. noch relativ faltig in der Ecke |
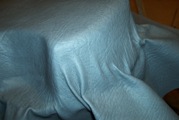
|
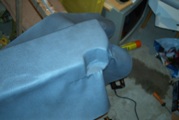
|
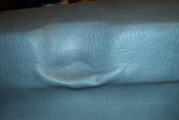
|
40. Die selben Falten nur näher |
41. Schon ralativ viel fest geklebt |
42. eine Aussparung für die Schrauben |
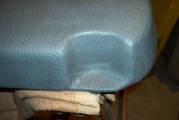
|
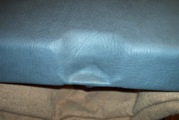
|
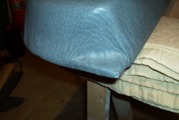
|
43. Die Ecke von vorhin, nun aber ohne Falten |
44. Die selbe Aussparung, aber ebenfalls ohne Falten |
45. Kein Vergleich zu vorher, fast faltenfrei |
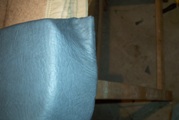
|
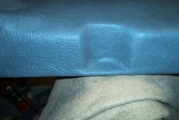
|
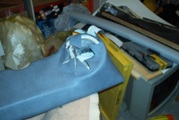
|
46. Nochmal die Ecke aus anderer Perspektive |
47. eine andere glatte Aussparung |
48. Der Ausschnitt für die Box |
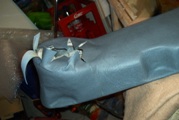
|
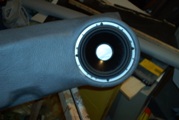
|
49. Die Einschnitte von der anderen Seiten |
50. Und so mit Box |
zu 37 - 47
Hier sieht man schön, wie das Doorboard bespannt wird.
Als erstes hat man den Kleber, den Pinsel und den Heißluftfön. Den Kleber habe ich zusammen mit dem Leder beim
Autosattler gekauft. Der Kleber wurde aus einem 10L Gebinde in mein Mitgebrachtes Kirschglas abgefüllt.
Das schwierigste ist, erstmal einen Anfang zu finden. Am besten fängt man mit der längsten, geraden Fläche an
Dafür bestreicht man die Fläche mit dem Kleber und lässt den ein bisschen (5 Minuten) ablüften. Anschließend
Legt man das Leder darauf und streicht es glatt. Ich habe mir für diesen Zweck eine Minirolle (Malerzubehör) ge-
kauft. Anschließend erwärmt man das Leder vorsichtig und gleichmäßig mit dem Heißluftfön und drückt dabei überall
mit dem Roller fest.
Ich habe die Erfahrung gemacht, dass es einfacher ist, das ganze Leder ersteinmal grob überall festzukleben. Die
Ecken sollte man dort wo Falten entstehen, nicht festkleben.
Wenn man alles soweit fest hat, kann man sich den Ecken zuwenden. Dies ist allerdings schlecht zu erklären, da es
sehr individuell ist.
Die generelle Vorgehensweise ist aber folgende:
Man muss immer Kleber auf die Fläche streichen, dann das Leder gut erwärmen und dann ziehen. Dabei versuchen festzu-
kleben. Hört sich ziemlich kompliziert an, aber irgendwann hat man den Dreh raus.
Wenn man die Boxen so angewickelt anbaut, wie ich das gemacht habe, kommt man um eine Schnittkante nicht herum.
Ich habe mich entschieden, die auf der späteren Unterseite zu machen, sodass man von oben kaum etwas sieht.
zu 48 - 50
Auf diesen Bildern kann man gut verfolgen, wie ich die Ausschnitte für die Box gemacht habe.
Auf dem Bild 49 sieht man zudem noch den Einschnitt, den ich machen musste, da es sonst nicht passte
Durch den überschüssigen Kleber sieht man den Schnitt noch sehr gut, nachdem ich den mit ein bisschen Verdünner
gereinigt hatte, war das gelbe auch weg.
Auf Bild 50 sieht man dann die eingesetzte, verschraubte Box.
Diese Site ist noch nicht vollständig
Bei Fragen steh ich gerne zur Verfügung und beantworte diese auch gerne.
spezial Thanks to "mrwoofa" bzw. "ghostfa" von www.motor-talk.de der mit sehr
geholfen hat (z.b. die Ringe hat er mir gefräst).
copyright by querys 2005